Whether you’re getting started with your warehouse barcoding, or are a seasoned professional looking for some quick tips, this article is for you. As always, our WMS Explained articles are more in-depth than our traditional content and are aimed at warehouse operators and current customers. Even if you are not using Descartes Peoplevox™ – yet – there should be some great actions for you to implement in your own warehouse.
A barcode is a simple yet powerful tool made up of lines of different widths that store information about whatever it’s attached to. In Descartes Peoplevox, barcodes usually represent items or locations in your warehouse, but they can be used for anything you need to track.
Think of barcodes as the IDs for everything in your warehouse. Descartes Peoplevox uses them to quickly and accurately track items and their locations, making it easier to keep things moving smoothly. To get the most out of the system, just make sure everything—every item and location—is labeled with a barcode.
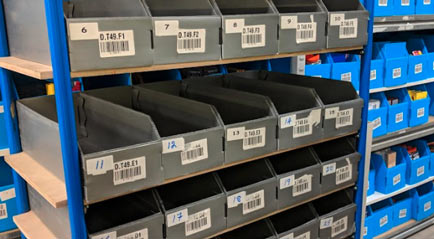
Organizing Your Warehouse Barcoding
To ensure smooth operations in your warehouse, each item code or SKU needs its own unique barcode. Depending on your current setup, here’s how you can organize your barcode labeling:
1. Items Already Barcode-Labeled and Recorded in Your Database
This is the ideal situation. Your product database is ready to be imported directly into Descartes Peoplevox.
2. Items Barcode-Labeled but Not Recorded in Your Database
If your items are already labeled but those barcodes aren’t recorded in your product database, you’ll need to capture and add them. Ask your suppliers for the SKUs/item codes along with their assigned barcodes. You can then export your product database to an Excel sheet, use a barcode scanner to input the barcode data, and re-import the updated database into Descartes Peoplevox.
3. Items Not Barcode-Labeled but Barcodes Are in Your Database
If you have barcode information in your database but the items themselves aren’t labeled, you’ll need to print and apply those labels. Import your product database into Descartes Peoplevox and use the system to print the necessary barcode labels.
4. Items Without Barcodes in Your Database or on the Items
The next steps depend on whether you manufacture these items or resell them:
- If You Manufacture or Own the Brand: It’s best to register with GS1 (the authority on barcodes) and assign EAN-13 barcodes to your products. This ensures that your items are properly labeled for retail and beyond.
- If You’re Reselling and Don’t Own the Brand: Request the EAN-13 retail barcodes from the manufacturer. If that’s not possible, you may need to assign your own barcodes. However, it’s crucial to coordinate with retailers to avoid conflicts with other products in their system.
- If You’re Importing and Not Selling to Retailers: You have the flexibility to create your own barcodes. The quickest method is to use your SKU number as the barcode. Just be aware of potential issues, like duplicate SKUs in your database or SKUs longer than 15 characters, which may not fit on your labels.
5. Items Share a Single Barcode Across Multiple Products
This situation usually happens due to supplier error. Each unique product needs its own barcode for inventory to be tracked accurately. Ask your suppliers to correct the barcodes, or apply new barcodes when the goods arrive.
6. Single Items with Multiple Barcodes
If an item has multiple barcodes because you source it from different suppliers, Descartes Peoplevox can handle this:
- Go to the Items tab in the Warehouse module.
- Select the item and click View.
- In the Edit item dialog, click Edit and then Suppliers.
- Enter the alternative barcode as a Manufacturer item number for each supplier.
- Click OK and Save.
If you have many items like this, consider importing an Item type suppliers file to streamline the process.
By following these steps, you’ll ensure that all items in your warehouse are properly barcoded and easily trackable in Descartes Peoplevox.
What Type of Barcode Should I Use?
Warehouse barcoding can be done in a variety of formats, each based on different symbologies, which are the rules for coding information into a pattern of bars and spaces. In Descartes Peoplevox, there are three main types of barcodes you can use, depending on your needs:
1. Code 128
- Description: This is a very high-density barcode symbology.
- What It Supports: Full ANSI character support, which includes numbers (0-9), letters (a-z, A-Z), and various characters and punctuation marks.
- When to Use It: If your item codes or SKUs are complex and include special characters, Code 128 is your best option.
2. Code 39
- Description: A variable-length, discrete barcode symbology.
- What It Supports: 39 characters, including uppercase letters (A-Z) and numbers (0-9).
- When to Use It: Code 39 is suitable for simple barcodes without special characters. Avoid using it for complex item codes.
3. EAN-13
- Description: A widely used barcode, especially in retail.
- What It Supports: Typically used for marking products sold in retail outlets to consumers.
- When to Use It: If your products are going to retail stores, EAN-13 is the standard to follow.
Use this guide to help you select the most appropriate barcode type for your operations in Descartes Peoplevox.
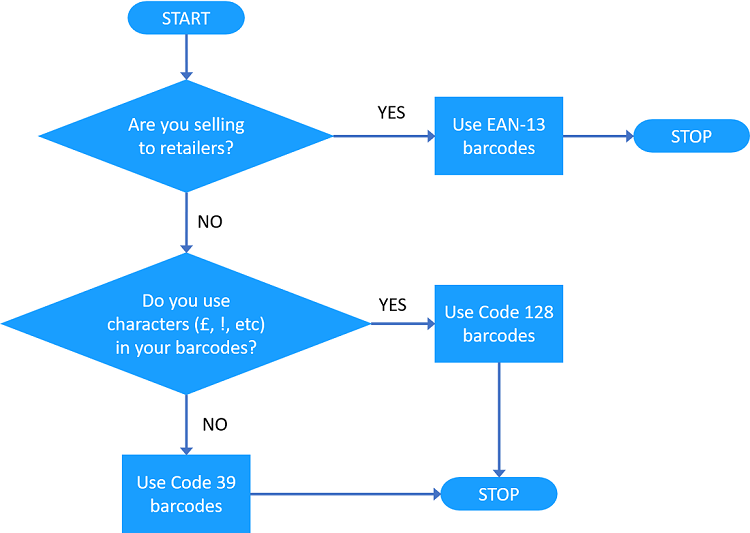
If you haven’t been sold yet on the value of barcodes in your warehouse…
Why is Warehouse Barcoding Important?
1. Enhanced Accuracy and Reduced Errors
Barcodes drastically reduce human error by automating data entry. Instead of manually typing in product details or quantities, warehouse staff can simply scan a barcode to record information instantly. This minimizes mistakes such as incorrect item entries or miscounts, ensuring that inventory records are precise. Over time, this accuracy builds trust in your inventory data, leading to better decision-making, fewer stock discrepancies, and improved customer satisfaction as orders are fulfilled correctly.
2. Increased Efficiency and Speed
Barcodes significantly speed up warehouse operations. Tasks like receiving goods, picking orders, and conducting stock counts are completed much faster with barcode scanning compared to manual methods. This boost in efficiency allows warehouses to handle more volume with the same resources, improving overall productivity. In fast-paced environments, this speed can be a competitive advantage, enabling quicker order processing and faster delivery times, which are critical in meeting customer expectations.
3. Real-Time Tracking and Visibility
Barcodes provide real-time tracking of inventory throughout the warehouse. As items are scanned at various stages—receiving, storing, moving, and shipping—the system updates instantly. This real-time visibility means you always know where each item is located, how much stock is available, and when you need to reorder. It also helps in quickly identifying and addressing issues like misplaced items or discrepancies in stock levels, ensuring that your inventory management is proactive and responsive.