The 6 Causes for Inventory Inaccuracy and why it is Killing Retailers
Picture this: A customer places an order online, excited about their purchase. But the next day, they get an email: “Sorry, your item is out of stock.” Frustrated, they take their money elsewhere, leaving a one-star review on the way out. Sound familiar?
This scenario happens all too often, and the culprit is nearly always the same: poor inventory accuracy leading to eroding profits, damaging customer trust, and creating chaos in the warehouse.
Let’s talk about the main causes of inventory inaccuracy and how to stop it for good.
The 6 Errors Killing Your Stock Accuracy
1. You don’t know what’s coming into your warehouse.
If your goods-in process is a guessing game, your stock counts will never add up. One missing item or an extra product sneaking in unnoticed can throw your entire inventory system off balance.
2. You lose track of items after they’re received.
Does this sound familiar? Goods come in, but instead of moving to a designated storage spot, they end up left somewhere “for now.” Without a clear assigned area, stock levels quickly spiral into chaos, and your pickers are left wondering where to pick orders from.
3. You’re stuck using paper.
Paper is holding you back. Mistakes pile up when your team has to scribble down notes, shuffle between forms, or manually update stock levels. It’s slow, inefficient, and painfully prone to error.
4. Your website is showing the wrong stock levels.
Nothing frustrates a customer more than placing an order only to be told the product isn’t available after all. Or, just as bad, you pull items offline too early and miss out on potential sales. Either way, inaccurate stock data leads to disappointed customers and lost revenue.
5. You can’t manage missing, damaged, or misplaced items.
When items disappear in the warehouse, you’re in trouble. A damaged product or a misplaced box throws off your entire operation, leaving orders unfulfilled and stock counts unreliable.
6. You don’t have live, actionable data.
Without the ability to pull real-time reports, you’re flying blind. Stock counts are outdated before they’re even complete, and identifying bottlenecks or errors becomes a Herculean task.
How to Fix Inventory Inaccuracy Problems (for Good)
The good news? Every one of these issues has a solution—and they’re easier to implement than you might think.
1. Nail Down Your Goods-In Process
Start strong by ensuring every item that enters your warehouse is accounted for. With a warehouse management system (WMS) that cross-checks deliveries against purchase orders, you’ll know exactly what’s arrived and what’s missing. No surprises, just accurate data
2. Track Every Movement
With a modern WMS, every item’s journey is logged in real-time. Scanners track where an item is picked up, where it’s moved, and where it’s stored. This eliminates the need for memory-reliant systems and keeps your team operating smoothly.
3. Say Goodbye to Paper for Good
Upgrade to a fully digital system that automates communication and updates inventory levels instantly. No more lost paperwork or manual errors—just efficient, streamlined operations. Review any process in your warehouse that requires any paper – and try and work out how to remove it.
4. Sync Your Website in Real-Time
Integrate your WMS with your ecommerce platform, like Shopify, to keep your website stock levels up-to-date moment by moment. Customers see exactly what’s available, and you avoid the embarrassment and lost revenue/damaged reputation of overselling or underselling products.
5. Handle Problems Before They Escalate
Equip your team with tools to handle missing or damaged items on the spot. With “skip functionality,” they can bypass an issue, alert the stock control team, and move on without grinding operations to a halt. The system will automatically adjust routes and inventory levels to maintain accuracy.
6. Leverage Live Reporting
A robust WMS gives you access to real-time dashboards and custom reports. Whether you need a quick overview or a deep dive into your stock levels, the data is always at your fingertips. With this level of visibility, you can identify and fix problems before they hurt your bottom line.
The Bottom Line.
Every warehouse faces challenges, but they don’t have to define your operations. By addressing these common errors and implementing modern solutions, you’ll take control of your stock, delight your customers, and drive your business forward.
A fundamental part of your warehouse operations to ensure accurate inventory is a regular and planned stock take. We have recorded a short video on how you would do a stock take with Peoplevox.
Your Next Move
Stock inaccuracy isn’t just a warehouse problem; it’s a business problem. It frustrates customers, costs you sales, and damages your reputation. But it doesn’t have to be this way.
With the right systems, processes, and mindset, you can turn your warehouse into a well-oiled machine. Say goodbye to frantic searches, overselling, and angry customers—and hello to accuracy, efficiency, and growth.
Ready to stop firefighting and start winning? Let’s fix your stock for good.
Take a Tour
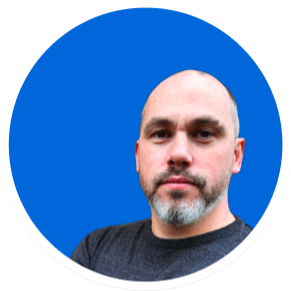