Running an efficient warehouse is crucial to staying competitive in today’s ecommerce driven environment. As businesses grow and consumer demand rises, optimizing every aspect of warehouse operations becomes essential. From the layout design to implementing automation, efficiency in the warehouse can make or break your bottom line.
This article explores the key strategies for enhancing warehouse efficiency, including how to keep on top of health and safety and reduce errors in the warehouse.
Table of Contents
- Optimize the layout of your warehouse
- Include automation sensibly throughout
- Forecast future demand to manage workflows
- Ensure effective inventory management
- Use technology to reduce errors
- Offer proper training for your staff
- Keep on top of health and safety
- Ensure the warehouse is kept secure
- Use efficiency containers, pallets and racks
- Use SKUs and batches
1. Optimize The Layout of Your Warehouse
One of the most impactful ways that you can improve the efficiency of your warehouse is by taking a look at the layout. Well-planned layouts will minimize travel time, reduce bottlenecks and improve general workflows. There are multiple ways that a warehouse can be organized, but a common approach is to include the items that get picked the most often close to the shipping and packing section of the warehouse. This will cut down on frequent extended trips and keeping these items at ergonomically sensible heights will reduce the strain on workers.
In addition to the floor layout, taking advantage of the vertical space is also a step that can greatly improve available space within the warehouse, without the need for lots of expansion. Keeping the aisles of your warehouse clean and wide enough for the machinery that may be passing through will work together to improve efficiency.
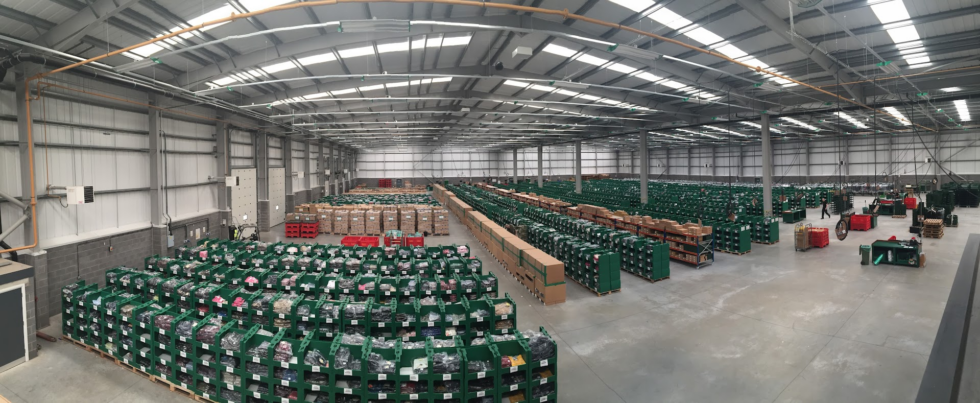
2. Include Automation Sensibly Throughout
There are an increasing number of warehouses taking advantage of automation to increase efficiency and the upfront investment required can often pay off in the long run. Automated guided vehicles and robotic picking systems can help speed up manual processes allowing staff to deal with more complex issues.
There are different levels of automation and the size of your operation will determine which level is appropriate. If you are running a smaller warehouse it may not be necessary to include full automation, but the sensible adoption of vertical lift modules for example could provide lots of benefits without too much cost.
3. Forecast Future Demand to Manage Workflows
Accurate demand forecasting can help you manage staff, stock and working hours to be as efficient as possible. Leveraging a warehouse management system can give you insight over time into when the busiest and less demanding periods are within a warehouse, and this gives you time to plan accordingly around your peaks.
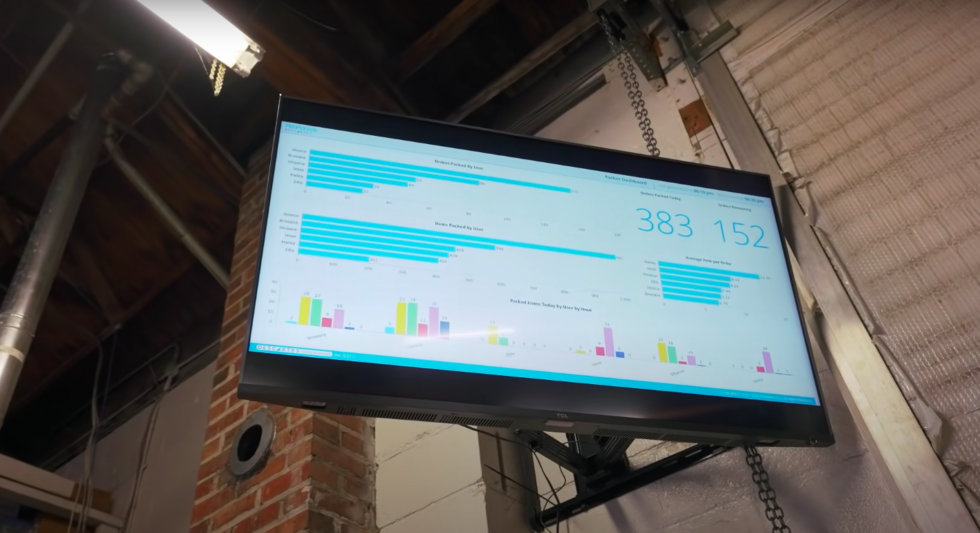
4. Ensure Effective Inventory Management
One of the most important elements of effective warehouse management is inventory management. Keep track of everything within the warehouse with robust systems, regular audits and depending on the size of your organization make sure you have an effective inventory management system in place. Leveraging techniques like ABC analysis will help you prioritize the right stock within your warehouse.
In ABC analysis, Items are divided into three categories. Category A includes high-value items with low sales frequency, meaning they require close monitoring and tight inventory control. Category B consists of moderate-value items with a balanced sales frequency, needing regular oversight. Category C includes low-value items with high sales frequency, which can be managed with more relaxed controls. This classification helps businesses prioritize resources and focus on the most critical inventory, optimizing storage space and reducing costs .
The above process can be completed manually if you want to take that route, but it may also be worth looking into an inventory management system that can take away a lot of the repetitive tasks necessary to run this system. This approach can also be done within a strong warehouse management system too.
5. Use Technology to Reduce Errors
Errors happen in warehouses and to some extent it’s impossible to cover everything, but an effective warehouse management strategy will help reduce the errors and have an immediate impact on the bottom line. Automated systems like barcode scanners, RFID tagging and effective WMS software will help you cut down on the most common errors in a warehouse.
Some of the most common errors include poor layout management, mis-picks when it comes to inventory and lack of proper planning around staff. Technology can help you here, but you need to ensure that the people in your warehouse are well looked after and know how to do the job too, leading onto the next tip, train your staff.
6. Offer Proper Training for Your Staff
Make sure that when you are implementing new systems and ways of working in a warehouse that the staff are thoroughly trained on what they need to do work within it effectively. This can include training around a new WMS that has been introduced, refresher courses on how to handle the products being shipped and how to work effectively with their colleagues. In addition to the more job focused training, health and safety training is also a key element that should not be ignored. Effectively communicating with your team through staff surveys can also help you improve the process. Having this process noted down will also help new staff members get up to speed with the systems that you operate.
7. Keep On Top of Health and Safety
Maintaining a strong focus on health and safety in your warehouse is vital for protecting both your workforce and your operations. Regular safety audits, proper signage, and adherence to regulatory standards like those set by OSHA help minimize the risk of accidents and ensure a safe working environment.
Make sure you have completed proper risk assessments for all relevant parts of the warehouse and that the staff have been given the training to keep both themselves safe and their co-workers.
8. Ensure the Warehouse is Kept Secure
Implementing the best practices shown above will not make much difference if you have an issue with items getting stolen within the warehouse. Using some of the most common security protocols including keycard or biometric scanners, access control systems, surveillance systems and fit for purpose alarms will help you manage the potential for criminal activity in and around the warehouse.
As part of the security process, regularly auditing your warehouses will help you keep on top of everything and make sure the systems are up to date. Making sure staff do the basics when it comes to keeping the workplace secure will also go a long way.
9. Use Efficient Containers, Pallets and Racks
The items you use to store stock within a warehouse also represent an opportunity to generate efficiencies. Using proper pallets, racks and optimizing the space that they take up will allow for easier handling and movement around the warehouses.
Higher racks can help you increase the vertical space availability for your goods whilst having containers and pallets that are well organized and easy to locate will also increase the picking efficiency for the stock they hold.

10. Use SKUs and Batches
Implementing a SKU (Stock Keeping Units) and batch tracking system will give you complete visibility over your stock and make your staff’s lives easier when it comes to finding the right item for shipment. Using the right SKUs will help you reduce errors and give you actionable data over time. Batch tracking will also help you maintain visibility over items in batches that may have specific use by dates or purchase dates, which is critical for quality control over time.
FAQs
How to calculate warehouse efficiency?
Warehouse efficiency can be calculated using the formula: Warehouse Efficiency (%) = (Total Productive Hours / Total Hours Worked) x 100. Total productive hours refer to the time spent on actual productive tasks such as picking, packing, and shipping, while total hours worked include all hours including downtime and non-productive activities.
This metric helps in identifying bottlenecks and areas for improvement to maximize operational efficiency. In addition to this, keeping a track of the most important warehouse KPIs will help you determine what areas of the warehouse are performing well and which areas need improvement.
How do vertical lift modules improve efficiency?
Vertical lift modules (VLMs) improve warehouse efficiency by maximizing vertical storage space, reducing the warehouse footprint, and speeding up the retrieval process. These automated systems bring the requested items directly to the operator, minimizing travel time and reducing labor costs. VLMs also improve inventory accuracy and can handle a wide variety of items, further enhancing overall operational efficiency.
Key Takeaways
- Make sure that you get your staff on board with any changes (especially big ones) that you are planning to make around how you organize your warehouse.
- Where necessary, explore technology based solutions that can help you optimize certain areas of your warehouse management.
- Always track the effectiveness of your warehouse operation, and just because you make a change doesn’t mean it’s a permanent fix. As new ways of thinking come out and new technology develops, it may be necessary to revisit the efficiency project in the future.